Анализ изображений
Анализ изображений (Цифровой анализ изображений, Анализ цифровых изображений) в материаловедении проводят с целью обнаружить и максимально точно выделить объект структуры для последующего качественного и количественного анализа.
Развитие информационных технологий и появление нового класса оптических микроскопов с электронной регистрацией изображений способствовали развитию исследований структуры материалов посредством компьютерных алгоритмов обработки цифровых изображений.
Процедура получения сведений об объектах микроструктуры с использованием методов анализа изображений состоит из следующих этапов:
- пробоподготовка;
- получение изображения объекта;
- анализ изображения объекта;
- анализ результатов измерений.
Все этапы нуждаются в проработке соответствующей методологии и стандартизации ее, т.е. разработке и принятии документов, детально описывающих порядок действий для достижения повторяемости и воспроизводимости результатов.
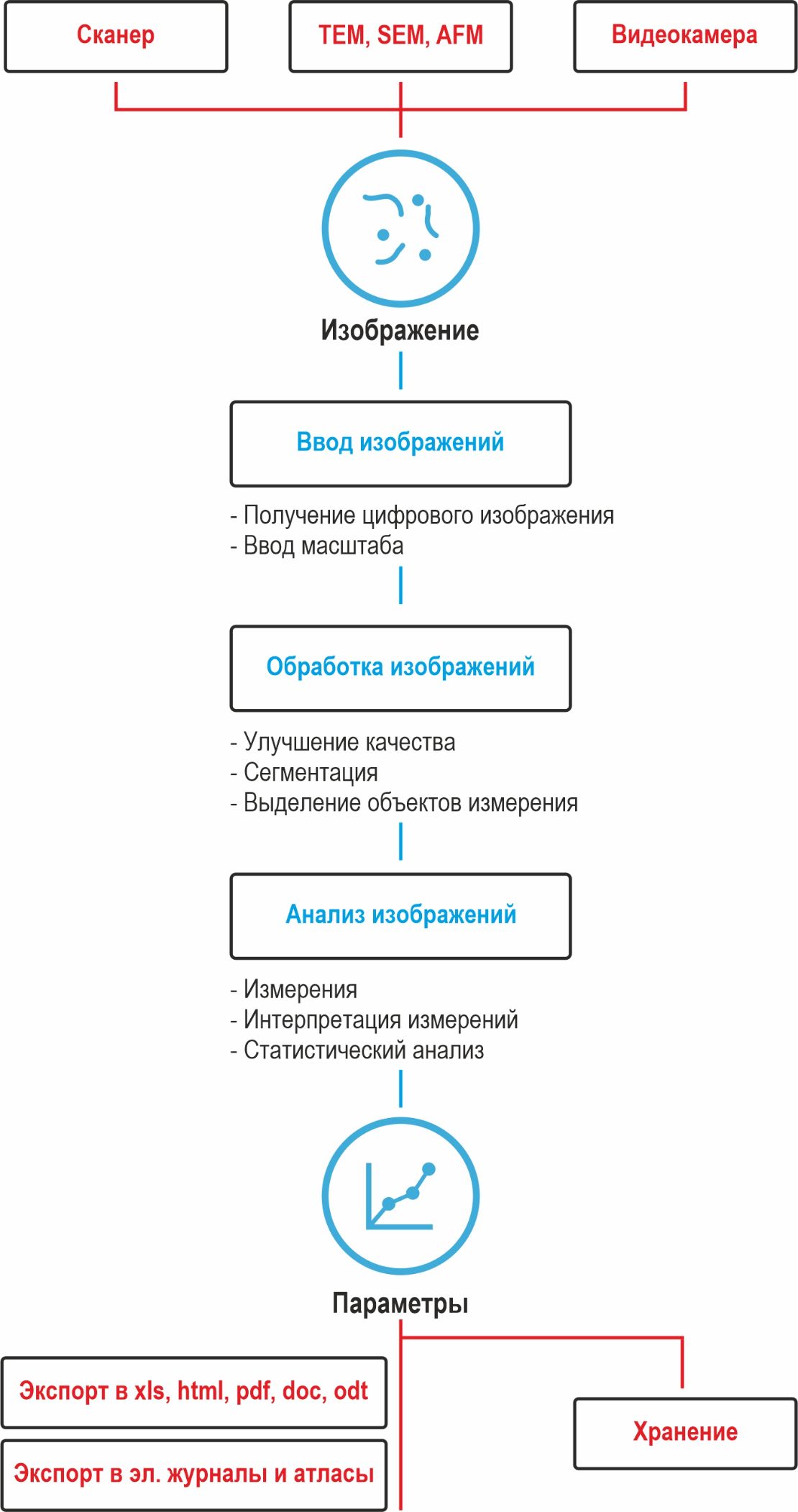
Анализ изображений структуры материалов относят к прямым методам исследования.
Существует три способа оценки структуры:
- Качественно-описательный способ. Используется как вспомогательный при составлении атласов изображений, для пояснения иллюстративного материала в научных статьях.
- Полуколичественная оценка - балльная оценка структуры в сравнении со структурами эталонных шкал (шкал типовых структур). Эти шкалы отражают величину зерен, форму, размеры и взаимное расположение структурных составляющих для различных сплавов и видам полуфабрикатов из них.
- Строго количественная оценка геометрических параметров.
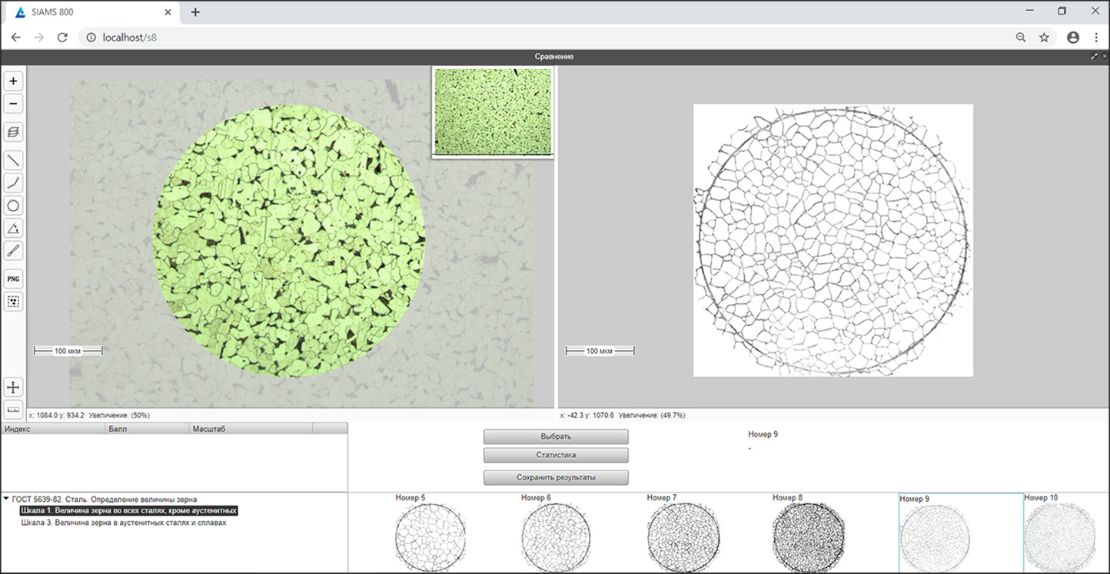
Ещё более оправданным выглядит использование систем анализа изображений для количественных методов оценки структуры материалов.
Основы количественного микроскопического анализа сформулировал в 1945 году С.А. Салтыков. Источником информации о параметрах пространственного строения по методу Салтыкова служат параметры двумерной структуры, измеряемые на плоскости шлифа, количественно взаимосвязанные с пространственными параметрами. Именно количественные данные о геометрических параметрах микроструктуры позволяют воспользоваться эффективным математическим аппаратом и вычислительной техникой для получения достоверных зависимостей между свойством и структурой материалов.
До появления систем анализа изображений количественная оценка структуры выполнялась «вручную» с помощью окулярных шкал и сеток, что было чрезвычайно трудоемко. Автоматизация анализа избавила оператора от рутинных подсчетов. Однако остались сложности, связанные с факторами, влияющими на изменчивость результатов измерений.
Автоматизированный анализ изображений чувствителен к качеству подготовки образца и оптике микроскопа, в случае анализа микроструктуры. Для обеспечения правильности результатов анализа и снижения погрешности измерений необходимо применять откалиброванную аналитическую систему и проводить анализ представительного участка микроструктуры.
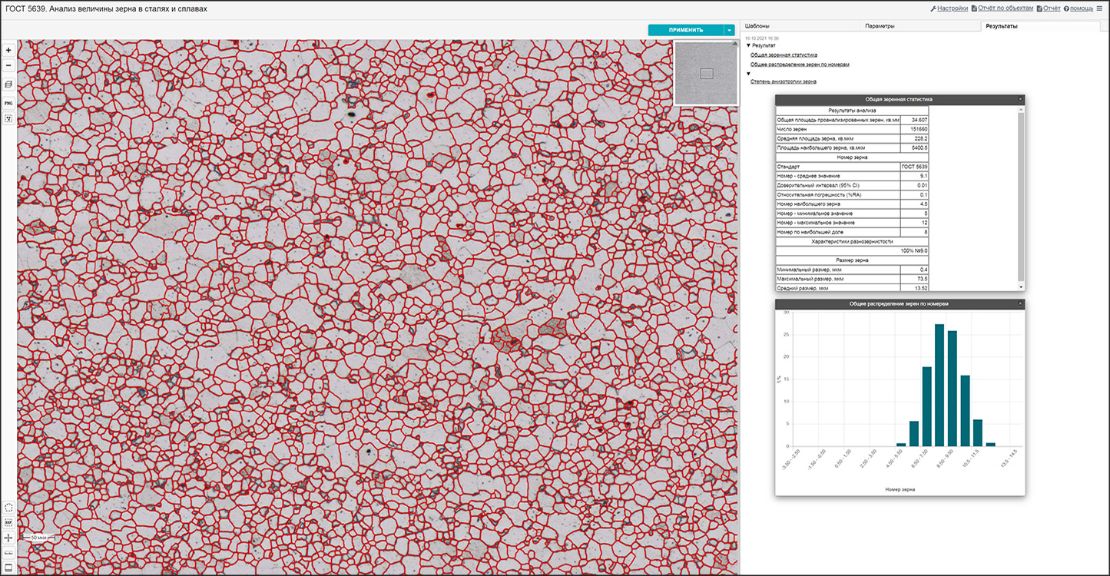
Литература
- Салтыков С.А. Стереометрическая металлография / С.А. Салтыков - М.: Металлургия, 1976. – 272 с.
- Металлографический анализ: история и перспективы развития / А. П. Михайлович, Т. А. Сивкова, Р. М. Кадушников, С. В. Сомина// Мир измерений. — 2014. — № 2. — С. 3-9.